Mu-HS1
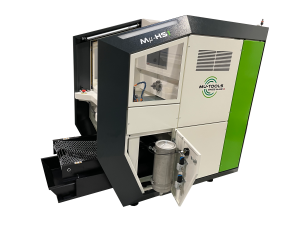
Important design features :
Very short installation and changeover times due to easy handling and accessibility.
Repetition accuracy to within 0.001 mm
Solid construction and optimised ergonomics
High precision production machine for small, medium and large series
Easy-to-use Beckhof interface and simple, intelligent parameterisation
Fast and self-centering honing tool attachment
High flexibility in changing settings from one type of workpiece to another
Large honing range Ø 0.6 – 80 mm
The table movement is driven by a linear motor, which allows a very precise positioning of the workpiece in the honing position and in the load/unload position.
Different honing stroke lengths can be set at different positions
For blind holes, 2 strokes movements can be programmed, in order to work more intensively on the bottom of a blind hole.
Different brands of honing tools are compatible, but the best results will be obtained with the original Mu-Tools SA honing tools.
NC control for the following functions:
Thanks to simple parameterisation, which does not require any special honing knowledge, accuracies of 0.001 mm are easily achieved.
Five different expansion options: constant speed, constant force, increment, touch and sizing.
An expansion backward and a fast expansion forward can be programmed, to avoid marks when removing the honing tool. This expansion is done at high speed and does not affect the cycle time.
The Beckhof control panel positioned at a short distance from the operator allows easy access to the programming.
A joystick positioned to the right of the operator allows direct access to the program, even during the cycle, to correct parameters.
Three control buttons above the joystick allow functions to be activated or deactivated or the final diameter of the part to be corrected in steps of 0.001 and 0.0001 mm
A quick approach of the honing tool with adjustment of the contact sensitivity allows to reduce the cycle times, when the honing tool does not touch the material yet. Once contact is made with the material, the expansion switches to its programmed working speed.
The expansion modes of the honing machines are either with a constant expansion speed variable from 1 sec. to 300 sec. for a gap of 0.01 mm diameter; during the lapping process the expansion pressure varies or with a constant expansion force, which is entered according to the diameter and size of the grains; during the lapping process, the expansion speed varies here. or in increments of X microns and during X table movement, which allows the tool to be lapped without too much effort in a long thin-walled workpiece for example. or by touching the honing tool in the bore and removing X microns. This mode is interesting for removing the same amount of material over and over again and where the diameter repeatability is less important. or by a single lapping movement (sizing) in order to calibrate parts to a high degree of accuracy.
A time delay at the end of the cycle can be set from a few seconds to several minutes to improve the surface finish of the bore or to polish. Once the final diameter has been reached and the delay time has elapsed, the honing tool deflates and the fixture automatically returns to the programmed load/unload position.
The Beckhof control panel allows several hundred programs to be saved and also allows programs to be exported or imported into an external system.
The programming software ensures that all the information required for a successful running-in cycle is set and automatically indicates if a parameter is missing.
The material removal is visible live during the process, as well as the expansion modes, the lapping time, the desired diameter and the number of lapped parts.
Decisive advantages of our NC honing system:
The micrometric expansion unit is directly integrated into the spindle and allows data to be retrieved from the expansion motor as well as the spindle motor. This data allows very fine tuning of the honing tools during machining.
The new technology of 3D printed fixtures allows a great reduction in the costs of clamping systems and very fast delivery times. Mu-Tools’ fixtures have a standard base, are easy to maintain and can be dismantled quickly. The clamping core, which holds the workpiece, is made of a two-component material as strong as aluminium. This part is therefore easily replaceable and allows greater flexibility with a single fitting.
The possibility of making Ø ± corrections in very fine steps of 0.001 or 0.0001 mm, even during the lapping process.
The honing tools are expanded evenly and absolutely parallel over the entire circumference. This also makes it possible to work without problems in interrupted-cut bores or with keys.
All honourable materials can be machined with the same tool.
As a manufacturer of honing tools for more than 75 years, Mu-Tools is able to produce all kinds of tools to suit your workpieces.
Length (mm) 1800
Width (mm) 1000
Height(mm) 1700
Weight (Kg) 900
Floor surface (m2) 1.8
Minimum air pressure (bar) 5.5
Power supply 400V AC — 50Hz
Multifunction touch screen control 15 ‘’
Honing range (mm) Ø 0.6 — 80 mm
Spindle height (mm) 130
Spindle speed (tr/min) 0 — 8000
Standard spindle motor torque (Nm) 11.4
Max. stroke length (mm) 350
Max. honing length (mm) 200
Max. table oscillation speed (m/s) 1.9
Light Led
Oil tank (l) 120
Filtering tissue (µm) 10-15
Colours (Ral) White 9010 / Black 7016 / Green 6038